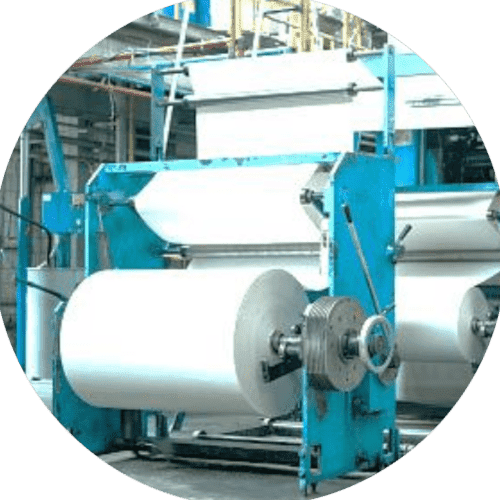
Technology
Grafiche Gelmini has a passion for technology embedded in its DNA. For many years, numerous projects have been executed by a highly skilled team of technicians.
The pre-press department is one of the company’s strengths, equipped with state-of-the-art tools capable of integrating and networking multiple platforms, such as MAC, Linux, and Windows.
In the production of our products, the most modern and effective printing techniques are used:
- Direct printing: A process in which large-format printing machines (plotters) print directly onto the substrate, typically fabric. The printing is done using four-color inkjet: yellow, magenta, cyan, and black (CMYK).
The quality and resolution are high, and the color can be printed without limits on quantity or number. It is also suitable for one-off prints, though not ideal for very large quantities; - Indirect printing: A technique where the image is not directly printed onto the final product but is first transferred onto other supports, such as rollers;
- Offset printing: An indirect printing technique where the image is first transferred from an aluminum sheet (plate) to a rubber cloth (blanket), and then impressed onto the substrate, such as a sheet of paper. Printing can occur on individual sheets or rolls.
In the case of sheets, the paper is taken from a stack and placed on a press bed with the help of vacuum and/or suction devices that prevent multiple sheets from entering. Then, it is aligned (register phase) to ensure precise printing and a perfect cut. Meanwhile, water-repellent ink, worked by rollers, is applied to the plate along with a layer of water to define the contours. The plate then transfers the ink to the rubber blanket, which receives the ink but not the water, and in turn, prints onto the paper sheet with the help of a cylinder.
Offset printing can achieve print runs of up to 50,000 copies per hour, maintaining consistent high-quality print resolution, even on irregular surfaces. However, it does not allow for heavy ink usage or delicate materials due to the pressure applied; - Flexographic printing: A direct printing technique that uses raised rubber or resin materials placed on plates (clichés). These print the image directly onto the substrate, with light pressure from a cylinder. Ink is applied to the plates via an Anilox roller made of steel or ceramic, engraved with cells that vary in number to control the amount of ink printed: the more cells, the better the detail.
In flexography, inks tend to dry quickly, making it ideal for printing on various materials, such as paper, aluminum, plastic materials, and even wood. Flexographic printing is mostly used for packaging, both in industrial and marketing contexts. It is now also used in newspaper printing, combined with other techniques; - Gravure printing: A direct printing technique that uses a metal roller coated with a thin copper layer, on which the design to be printed is engraved. The engraving is done through a system of cells of varying depths: the deeper the cells, the more ink is applied, and the darker the result. The cells are inked from an inkwell, and excess ink is removed by a doctor blade. After this phase, the roller transfers the ink directly onto the substrate.
Gravure printing is commonly used for high-volume magazine printing; - Screen printing: A printing technique that uses a polyester, steel, or nylon mesh screen stretched over a frame made of aluminum, metal, or wood (screen printing frame). It is based on permeography, a process of waterproofing specific areas of the screen. During printing, the screen is lowered onto the substrate, and ink is poured onto the screen. A bar then presses the ink through the screen into the free areas, transferring it to the substrate.
Screen printing can be repeated cyclically, achieving high production speeds. It can be used on any substrate and is the only technique capable of producing special effects with specific inks, such as raised, glitter, iridescent, or photochromic inks. Screen printing offers high color accuracy and durability over time. It is the most widely used technique globally for textile printing; - Pad printing: An indirect printing technique that uses a silicone pad. The printing process begins with engraving the image on a steel or resin plate (pad printing cliché), which is then coated with indelible ink. The pad is pressed against the plate to collect the ink and transfer it to the substrate. Because the silicone pad is very soft, it adapts to surfaces of various shapes, such as those of pencils.
Pad printing, compared to screen printing, provides better definition, ensuring sharper reproduction of even fine details.
The client is guaranteed the regular and precise use of the declared materials. Grafiche Gelmini rejects the use of inconsistent or “polluted” papers, such as those mixed with other materials to reduce production costs or quality.
Pallets are designed with special packaging to ensure perfect preservation of the finished product from humidity and environmental factors during transport and storage.
In this regard, Grafiche Gelmini was one of the first companies in Italy to use shrink film for packaging its products, ensuring their preservation over time.
Every aspect is carefully monitored and guaranteed, from production to shipping: the reliability of the goods is a cornerstone of our corporate philosophy.